Asphalt Industry
Wear protection in the asphalt industry – conveying, mixing, crushing and screening
In asphalt production and transportation, wear is relatively common because asphalt itself is an abrasive material, to which other similarly wear-causing fractions are then often added. In addition, asphalt is produced and processed at high temperatures, which literally creates “softening conditions” for common metals, such as steel. This calls for the use of special wear-resistant, hard steels such as Hardox. For service life extension of machines and installations in asphalt production and transport, Wivé Techniek also applies various other wear-resistant materials.
Applications of wear protection in asphalt production and transportation
We clad the walls of front dosers with our plastic HMPE wear plate WearProtect PE or the wear-resistant fine-grained steel grade WearProtect WPS, similar to Hardox. Conveyor belts receive a side guide made of Rubber, and at transfer points we apply natural rubber types, such as Racloprema. If necessary, we can also use Feraser belt scrapers. In the ladder conveyor, the elevator bodies are completely replaced with weld-on plates from our WearProtect WMW program or welded on with wear-resistant weld-on wire (WearProtect LTM). In the conveyor screw, we make blades from wear-resistant welded-on plates and also clad the trough with segments from armor plate WearProtect WMW. We can use the same material as cladding for the chute and cube valves.
Wear in asphalt crushing and screening
For PR roller crushers, we have wear-resistant cast steel solutions from WearProtect WMC, while for asphalt screening we supply specially manufactured heat-resistant screening decks, in any specification.
Wear protection in asphalt drying drums and vanes
The drying process takes a very heavy toll on all the materials used, due to the heat and continuous “shoveling” of the asphalt. A recipe for intense wear and tear. For the white drum, we install spreader vanes from WearProtect WPS. For the black drum, we recommend inlet and feed vanes made of wear-resistant welded-on plates. In connection with the predictable wear period, we have devised a special exchange system for these vanes that turns the production stop into a “pit stop”.
Want to know more about wear protection in the asphalt industry?
Be sure to contact us!
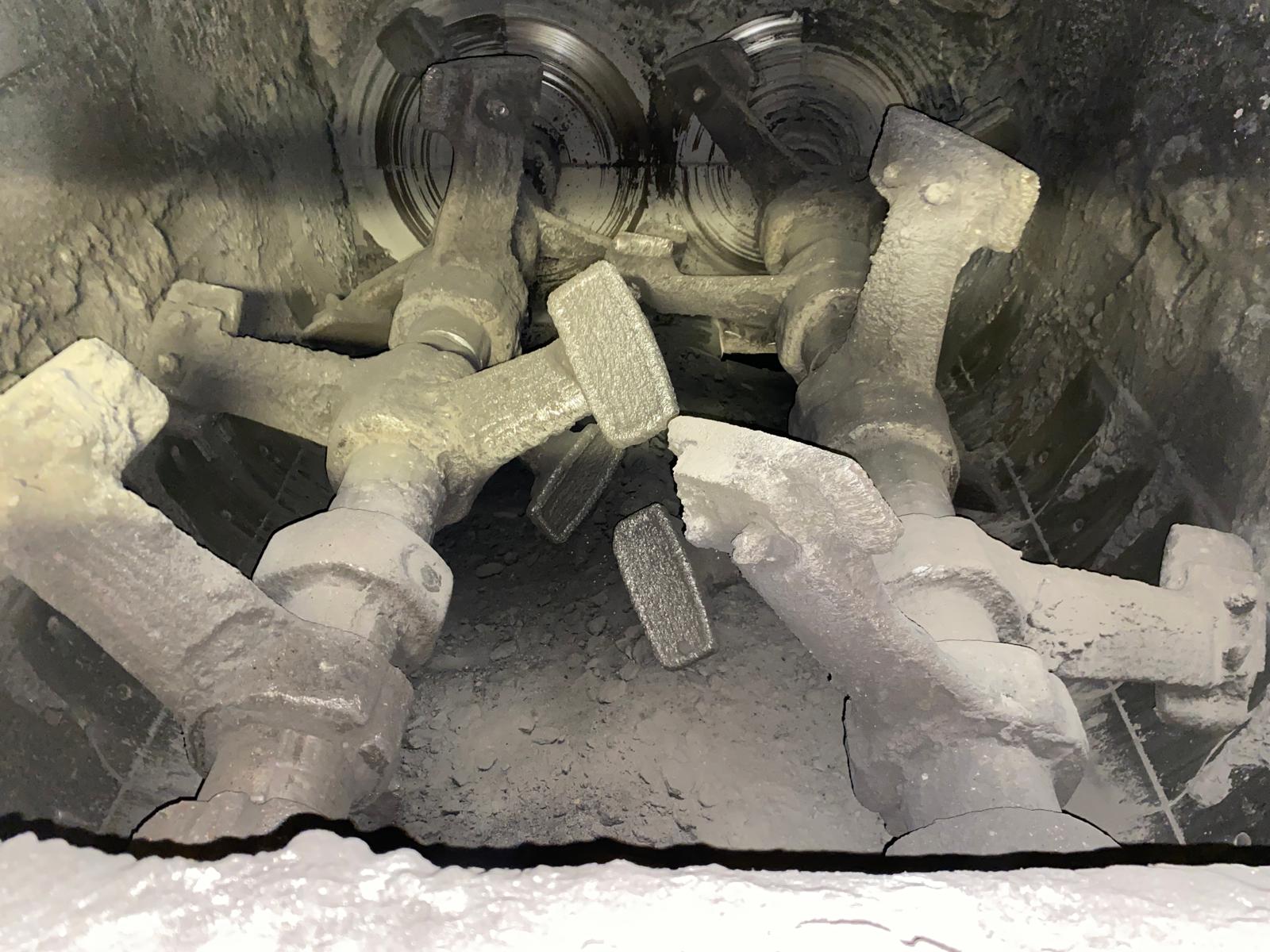